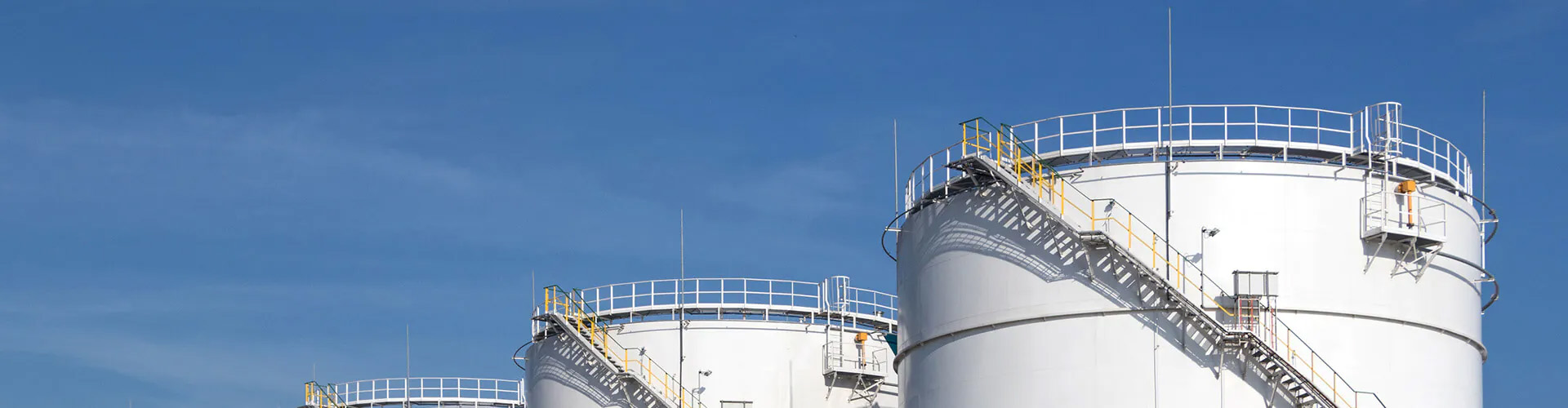
Download the pdf file by clicking here
Tank Storage Association Insight Magazine Autumn 2024, Issue 19
THE TANK TERMINALS OF THE FUTURE: A VISION POWERED BY DIGITAL TWINS
As digital twin technology continues to evolve, the tank terminals of the future will be characterized by unprecedented levels of efficiency, safety, and sustainability. The industrial landscape is undergoing a rapid transformation, and the tank terminal industry is no exception. As the demand for storage and handling of liquid and gaseous products continues to rise, the industry faces increasing pressure to enhance efficiency, safety, and sustainability. Digital twin technology is emerging as a key enabler in this evolution, offering unprecedented opportunities to revolutionize the way tank terminals operate. This article explores the vision of the tank terminals of the future, powered by digital twins, and the profound impact this technology will have on the industry.
Understanding Digital Twins
A digital twin is a virtual replica of a physical asset, system, or process, created using real-time data and advanced simulations. It provides a dynamic, real-time representation of the physical world, enabling operators to monitor, analyze, and optimize their assets remotely. In the context of tank terminals, digital twins can encompass everything from storage tanks and pipelines to control systems and safety protocols.
The Challenges Faced by Tank Terminals Today
Tank terminals play a crucial role in the storage and distribution of a wide range of products, including petroleum, chemicals, and liquefied natural gas. However, the industry faces several challenges that hinder its efficiency and sustainability:
Aging Infrastructure: Many tank terminals operate with aging infrastructure that requires frequent maintenance and upgrades.
Safety Concerns: The handling of hazardous materials poses significant safety risks, necessitating stringent safety protocols and real-time monitoring.
Environmental Regulations: Increasingly stringent environmental regulations demand better monitoring and management of emissions and spills.
Operational Inefficiencies: Manual inspections and maintenance procedures can be time-consuming and prone to human error.
Data Silos: Disparate systems and data silos make it challenging to obtain a comprehensive view of terminal operations.
The Role of Digital Twins in Addressing These Challenges
Digital twin technology offers a holistic solution to the challenges faced by tank terminals. By creating a digital replica of the entire terminal, operators can gain real-time insights into the condition and performance of their assets. Here’s how digital twins are set to transform the tank terminal industry:
Enhanced Asset Management
Digital twins provide a comprehensive view of all assets within a tank terminal, including their condition, performance, and maintenance history. This enables predictive maintenance, where potential issues are identified and addressed before they lead to costly downtime or accidents. For example, sensors installed on storage tanks can monitor parameters such as temperature, pressure, and corrosion levels, feeding this data into the digital twin. Machine learning algorithms can then predict when maintenance is needed, optimizing the maintenance schedule and reducing unplanned outages.
Improved Safety and Compliance
Safety is paramount in tank terminal operations. Digital twins enhance safety by enabling real-time monitoring and simulation of various scenarios. Operators can use the digital twin to simulate emergency situations, such as leaks or fires, and develop effective response strategies. Additionally, digital twins can help ensure compliance with environmental regulations by continuously monitoring emissions and detecting any deviations from acceptable levels. This proactive approach not only enhances safety but also helps avoid regulatory fines and penalties.
Operational Efficiency
Digital twins streamline operations by automating routine tasks and providing actionable insights. For instance, digital twins can automate the scheduling of product transfers, optimizing the use of storage space and minimizing the risk of contamination. They can also monitor energy consumption and identify opportunities for energy savings, contributing to overall operational efficiency. By integrating data from various sources, digital twins eliminate data silos and provide a unified view of terminal operations, enabling better decision-making.
Remote Monitoring and Management
One of the most significant advantages of digital twins is their ability to facilitate remote monitoring and management. Operators can access the digital twin from anywhere, using a computer or mobile device, and obtain real-time information about the terminal’s status. This is particularly valuable for terminals located in remote or hazardous areas, where on-site inspections can be challenging. Remote monitoring also enables rapid response to issues, reducing downtime and enhancing operational resilience.
Training and Simulation
Digital twins serve as powerful training tools, allowing operators to gain hands-on experience in a virtual environment. New employees can use the digital twin to familiarize themselves with the terminal’s layout and operations without the risks associated with real-world training. Additionally, digital twins can be used to simulate various operational scenarios, helping operators develop the skills needed to handle complex situations. This improves overall workforce competency and preparedness.
The Future of Tank Terminals: A Digital Twin Vision
As digital twin technology continues to evolve, the tank terminals of the future will be characterized by unprecedented levels of efficiency, safety, and sustainability. Gizil GmbH’s Virtual Plant is at the forefront of this transformation, offering a comprehensive platform that integrates real-time data, advanced analytics, and user-friendly interfaces to revolutionize tank terminal operations. Here’s a glimpse of what this future might look like with Virtual Plant leading the way:
Smart Terminals
Virtual Plant equips tank terminals with a network of interconnected sensors and devices, creating a fully integrated digital ecosystem. The digital twin, powered by this platform, serves as the central hub, aggregating data from all sensors and providing a real-time view of terminal operations. Smart algorithms continuously analyze this data, identifying opportunities for optimization and providing actionable insights to operators, resulting in improved efficiency and reduced operational costs.
Static Digital Twin as a Single Source of Truth
The concept of a static digital twin, where a digital replica of the terminal’s physical and static assets is maintained as a single source of truth, is crucial for ensuring data accuracy and accessibility. This static digital twin includes detailed information about the terminal’s infrastructure, layout, and equipment, which can be accessed and updated in real-time.
Benefits:
Data integrity: All stakeholders access the same up-to-date information, reducing errors caused by outdated or conflicting data.
Simplified maintenance: Maintenance schedules and records are easily managed, ensuring timely interventions and reducing downtime.
Regulatory compliance: Simplifies reporting and compliance by maintaining accurate and comprehensive records of terminal operations and equipment.
Sustainable Practices
Sustainability is a core focus of Virtual Plant. Digital twins help minimize environmental impact by optimizing energy consumption, reducing emissions, and preventing spills. The platform provides continuous monitoring and reporting, ensuring compliance with environmental regulations. By integrating sustainable practices into daily operations, tank terminals can improve their environmental footprint, enhance their reputation, and meet the expectations of stakeholders.
Enhanced Collaboration
Virtual Plant facilitates enhanced collaboration between different stakeholders, including terminal operators, maintenance teams, regulatory authorities, and customers. By providing a single source of truth, this digital twin platform ensures that all parties have access to accurate and up-to-date information. Improved coordination and decision-making lead to more efficient operations, quicker response times, and stronger relationships with partners and customers.
Conclusion
The tank terminals of the future, powered by digital twin technology and Virtual Plant, represent a paradigm shift in the way industrial operations are managed. By providing a comprehensive and real-time view of terminal operations, this platform enables enhanced asset management, improved safety, operational efficiency, and sustainability. As the industry continues to embrace this technology, tank terminals will become smarter, more autonomous, and more resilient, driving significant value for operators and stakeholders alike. In embracing Virtual Plant and digital twin technology, tank terminals are not just adapting to the future - they are shaping it. The journey towards fully integrated, efficient, and sustainable operations is well underway, and the vision of the tank terminals of the future is closer to becoming a reality. Virtual Plant stands ready to lead this transformation, delivering the tools and insights necessary to thrive in the evolving industrial landscape.
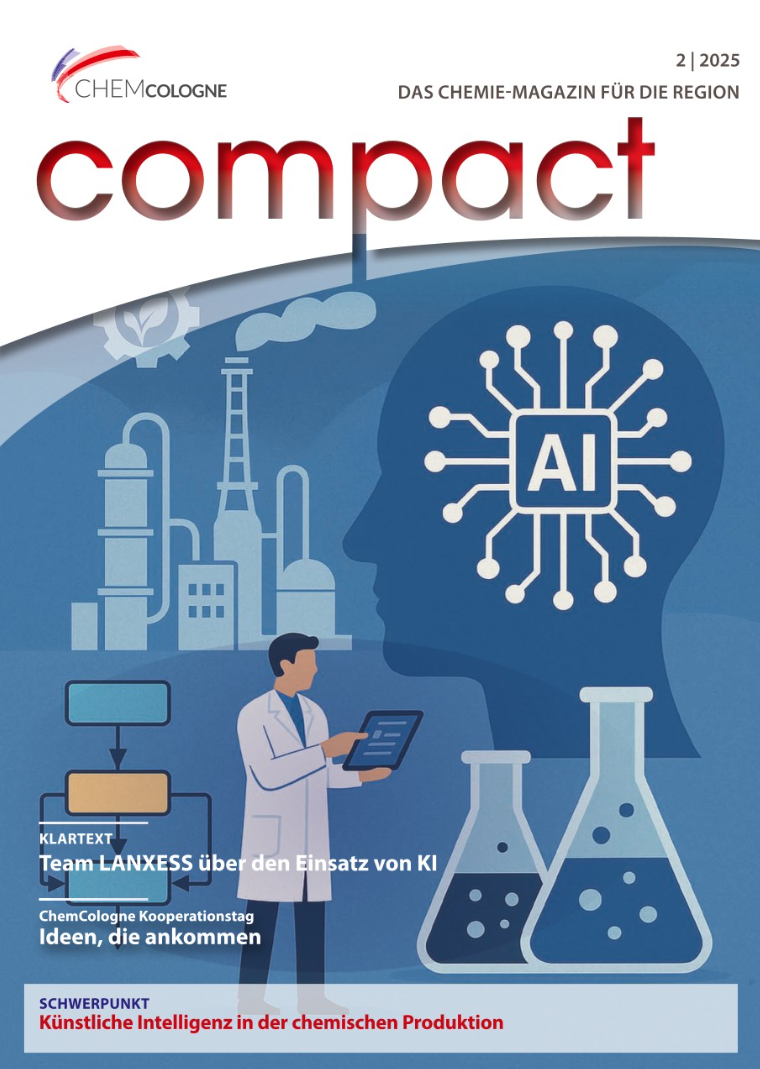
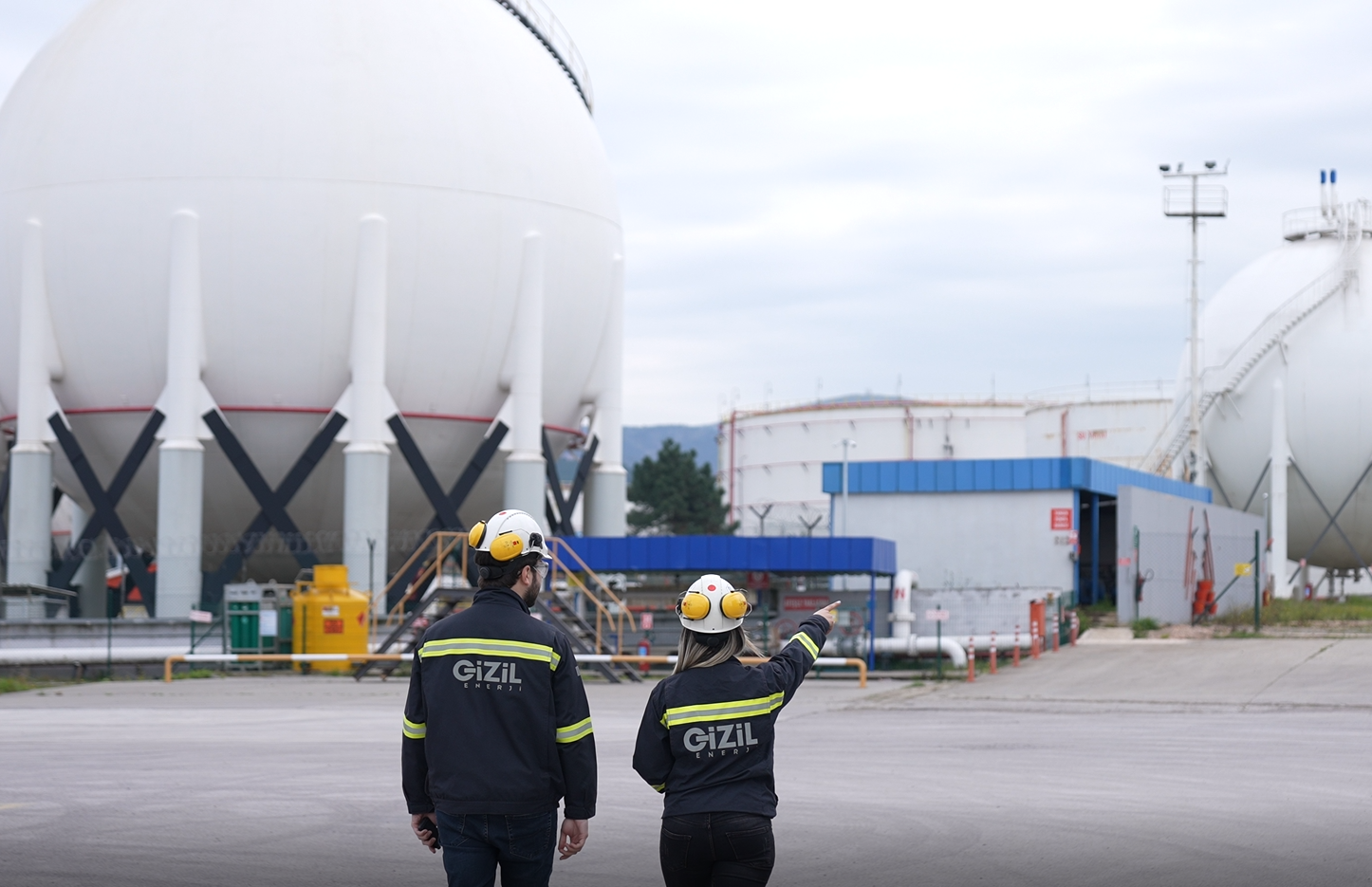