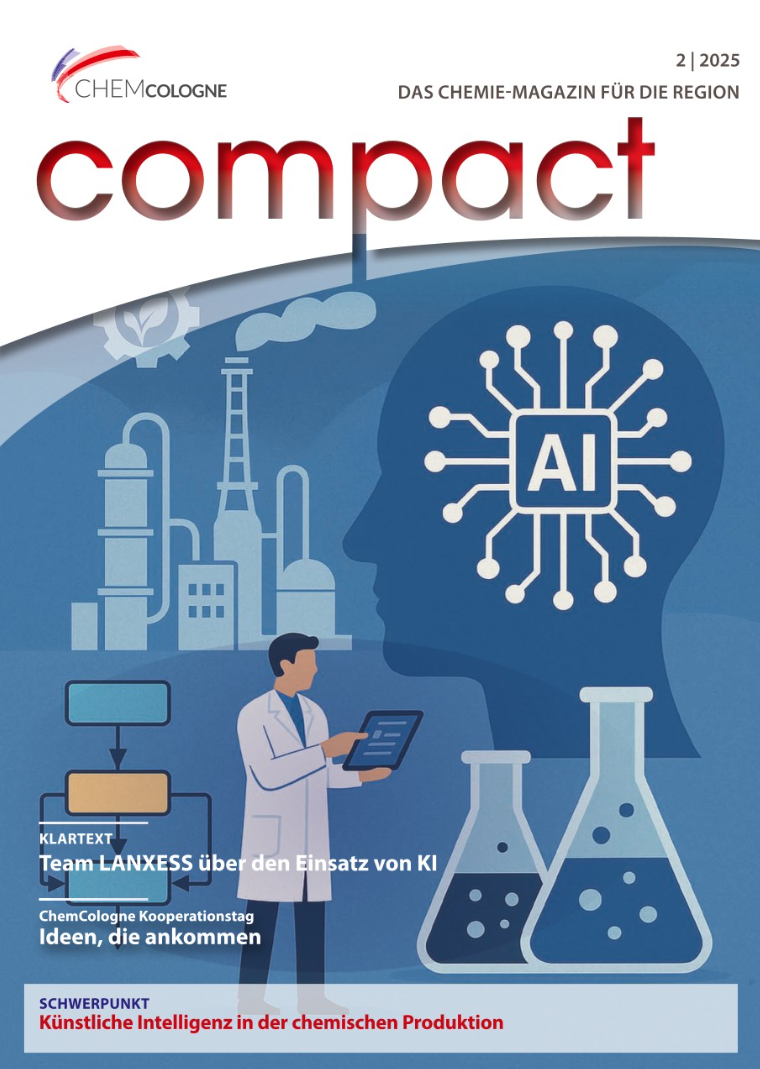
Download the pdf file by clicking here
ChemCologne Compact 2/25
Artificial Intelligence in Chemical Production
How AI and Virtual Plants Are Modernizing Chemical Production
Aging plants, growing pressure
The German chemical industry is under increasing pressure. Geopolitical upheavals, volatile energy markets, and sharply rising producer prices are straining the sector. At the same time, the EU Green Deal, adopted in January 2023, has set a clear course:
The industry must significantly reduce its CO₂ emissions — and do so in a very short time.
Chemical companies now face the challenge of meeting climate targets while operating with ever-thinner margins and growing complexity.
One key but often underestimated challenge is the age of the industrial infrastructure. Many plants date back to a time when digitalization played no role. This gap between the ambition for climate protection and the reality of outdated, often poorly documented plants is significantly slowing necessary progress.
This is where Gizil’s Virtual Plant comes in. It’s not a conventional simulation tool, but a digital twin focused on the physical reality of industrial sites.
⸻
A precise replica in a fraction of the time
Using 3D laser scans, technical documentation, and AI-supported mapping of the actual plant conditions, a precise digital replica of existing facilities is created.
Static and dynamic data, documents, and other asset metadata are intelligently linked to the plant’s 3D representation (e.g., point clouds or 3D models).
For example, complex piping systems can be (semi-)automatically identified and digitized.
Beyond that, AI-driven contextualization enables significantly faster orientation and data assignment within the digital plant model. Already today — and even more so with the functions currently under development — the digital documentation process and information delivery can be accelerated by a factor of 10 to 20 compared to conventional methods.
⸻
A visual platform for interdisciplinary collaboration
In contrast to digital process models that simulate chemical flows or control loops, the Virtual Plant provides transparency about the real-world condition of the plant.
Teams from engineering, maintenance, and occupational safety can virtually walk through the facility, locate nameplates, plan maintenance tasks, and track changes to the physical setup — all without setting foot in the plant.
This makes the Virtual Plant a visual platform for interdisciplinary collaboration during shutdowns, retrofits, safety inspections, and regulatory compliance.
⸻
Ready for the digital future
The Virtual Plant offers clear advantages:
Planning processes for modifications and upgrades are significantly accelerated, and workplace safety is improved as on-site interventions are reduced. Additionally, plants can be operated longer and decisions can be made more sustainably and with better information.
Conclusion: In a time when inaction comes at a high cost and the green transition is unavoidable, the Virtual Plant offers the chemical industry a fast, practical solution. It creates operational clarity and prepares existing plants for the digital future.
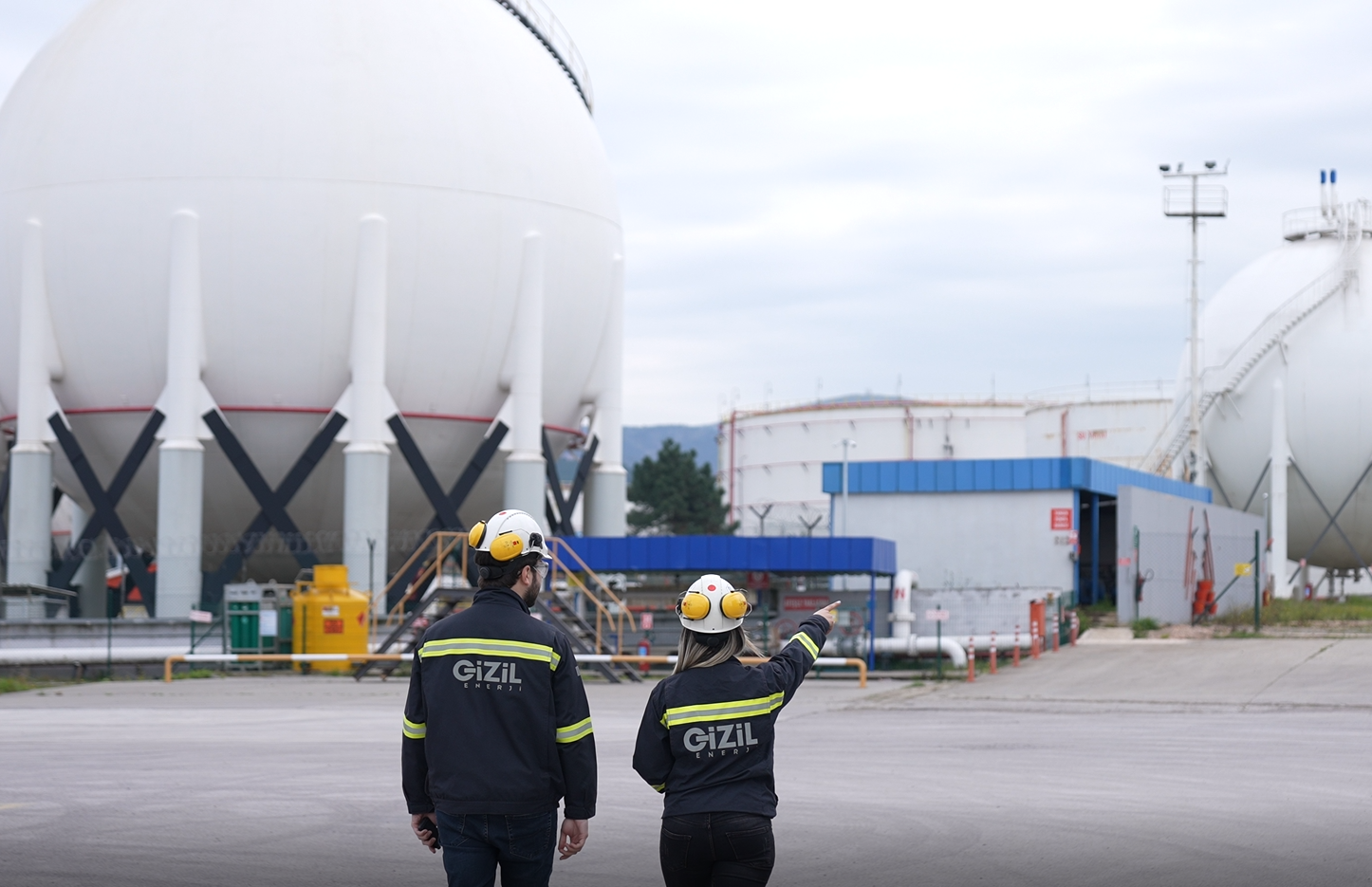
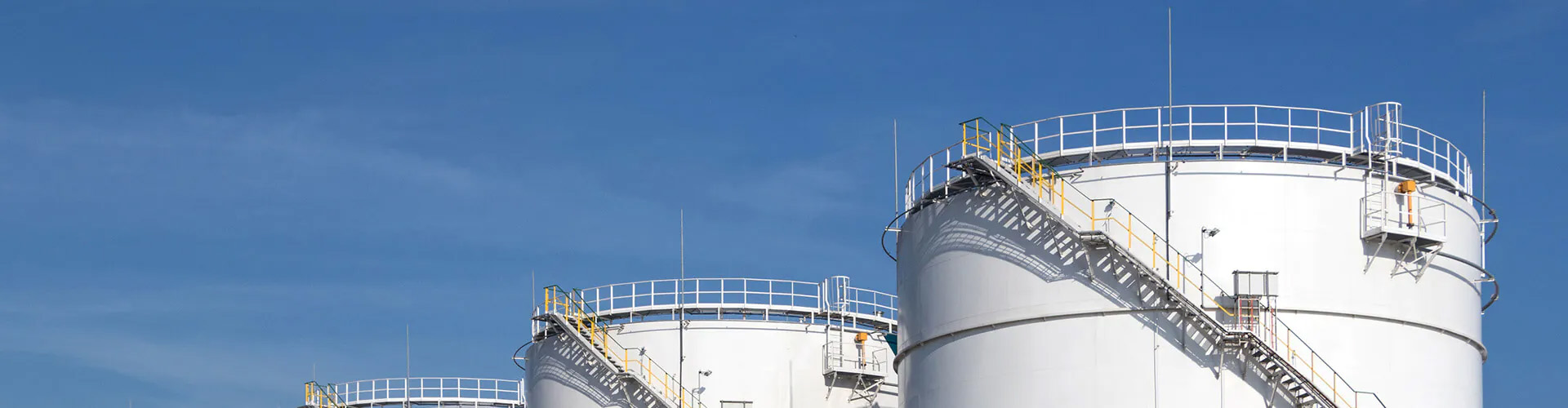